Diecasting is a highly sophisticated manufacturing technique that plays a crucial role in the production of complex metal components with accuracy and precision. This technique involves injecting the molten metal in a mold cavity under high pressure, making it possible to create complex shapes and elaborate patterns that would be difficult to accomplish using other methods. Diecasting is used extensively in various industries, including electronic, aerospace, automotive, and consumer goods, because of its effectiveness as well as its ability to make top-quality components. This article explains the intricacies involved with diecasting by detailing its process, benefits, and potential applications.
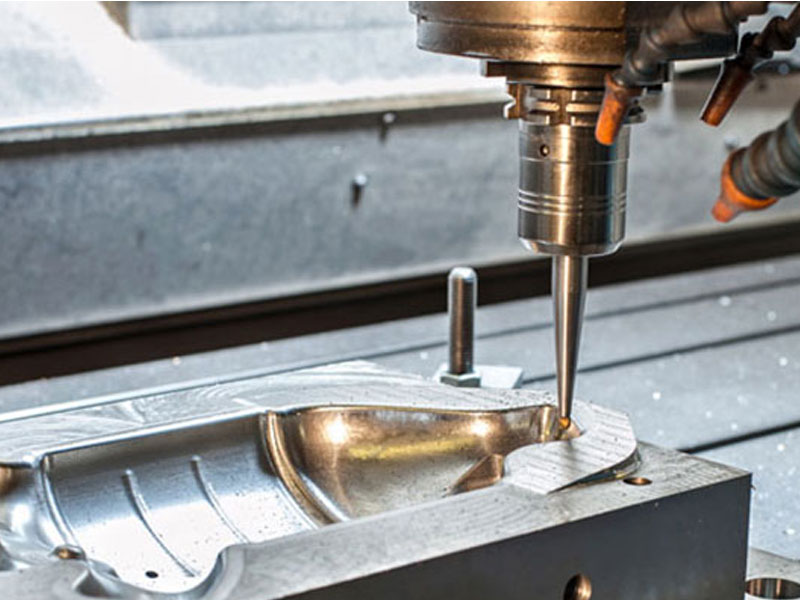
Diecasting starts by creating molds, also referred to as a"die," which typically is made from toughened steel. The mold is designed to stand up to the temperatures and pressures involved in the process. When the die is in place, molten metal, usually made up of aluminum, magnesium, zinc, or copper, is heated to the state of liquid and injected into the mold cavity with high pressure. The pressure will remain constant until the metal is solidified ensuring that the molten metal covers every inch of the mold, with intricate design and thin walls. After the metal has cooled and formed, the mold is open, and the final part is ejected. This technique allows for high efficiency and accuracy when making metal parts.
One of the major benefits of diecasting is its effectiveness in the production of mass quantities. When the dies are made it can be repeated hundreds, or even thousands of instances with very little variation between pieces. This is vital when it comes to industries that require massive numbers of components that are identical. Diecasting is also known for its material efficiency. This process produces lesser waste than other techniques for forming metal because excess metal can be recycled and used again. This not only reduces cost of materials but it is also a part of environmentally sustainable manufacturing techniques. A combination of the speed, precision and high efficiency in the production of materials makes diecasting a desirable alternative for large-scale production.
Diecasting is extensively used in various industries due to its versatility and the range of different materials used. In the automobile industry diecast parts are vital in the production of components such as motor blocks, transmission casings, and structural parts. The aerospace industry has a dependence on diecasting to create lightweight, high-strength parts that can stand up to the rigorous conditions of flying. In consumer electronics, diecast parts are utilized for frames and frames that provide durability and precision in devices. Diecasting's range of applications extends to applications in the telecom, medical and power tools sectors which shows its wide-ranging application and value. To gather additional information please navigate to these guys
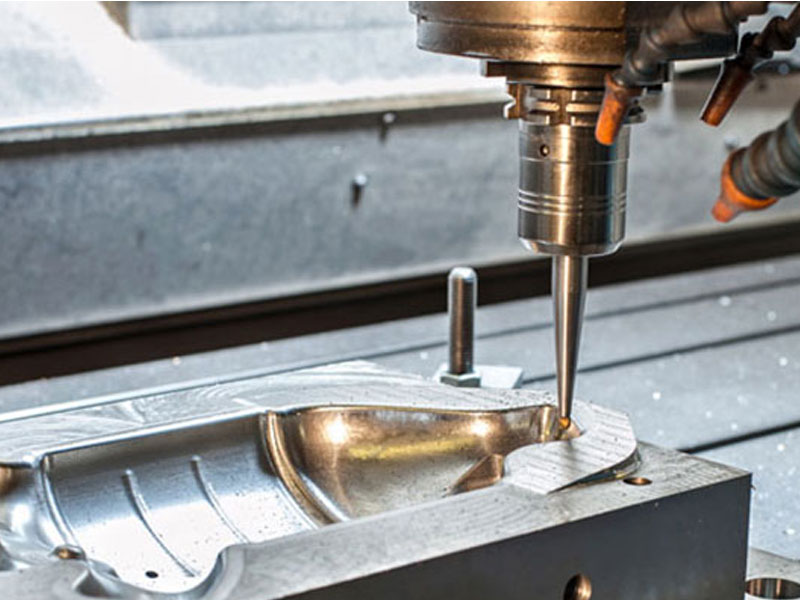
The selection of the materials used in diecasting can significantly affect the physical properties and efficiency of the final product. Aluminum is one of the top choices because of its superior strength-to-weight ratio, resistance to corrosion, along with its excellent electrical and thermal conductivity. These qualities make aluminum an ideal choice for aerospace and automotive uses in which weight reduction is essential. Zinc alloys are strong and ductility. This makes them perfect for applications that require precise specifications and durability. Magnesium alloys are the lightest steels that can be used for structural purposes, giving an advantage in applications where the weight savings are crucial. Copper alloys, while more rarely used but are coveted for their outstanding electrical conductivity and their resistance to corrosion. Each one of them has its own advantages making it possible for manufacturers to pick the best option for their particular application requirements.
Diecasting is a critical manufacturing process that enables the manufacture of precise, top-quality metal parts for various industries. Its capability to make intricate designs with high-quality tolerances and smooth finish makes it indispensable for applications requiring intricate details and consistent quality. Efficiency and value-for-money of diecasting add to its value and support mass production while keeping high quality standards. Technology advances, and the demand for reliable robust, lightweight and long-lasting components expands, diecasting will remain the foundation of modern manufacturing, driving innovation and excellence in production.